

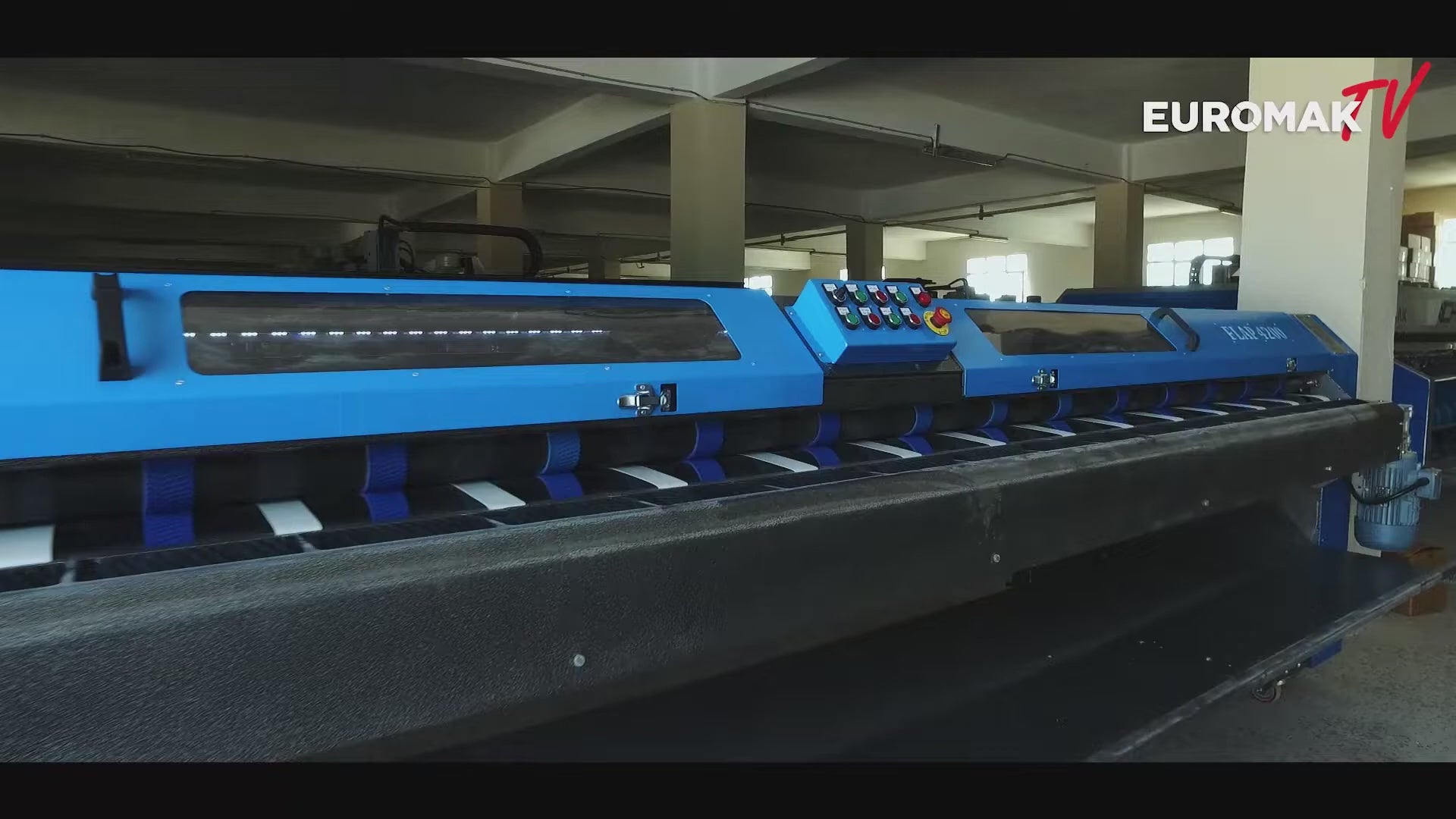

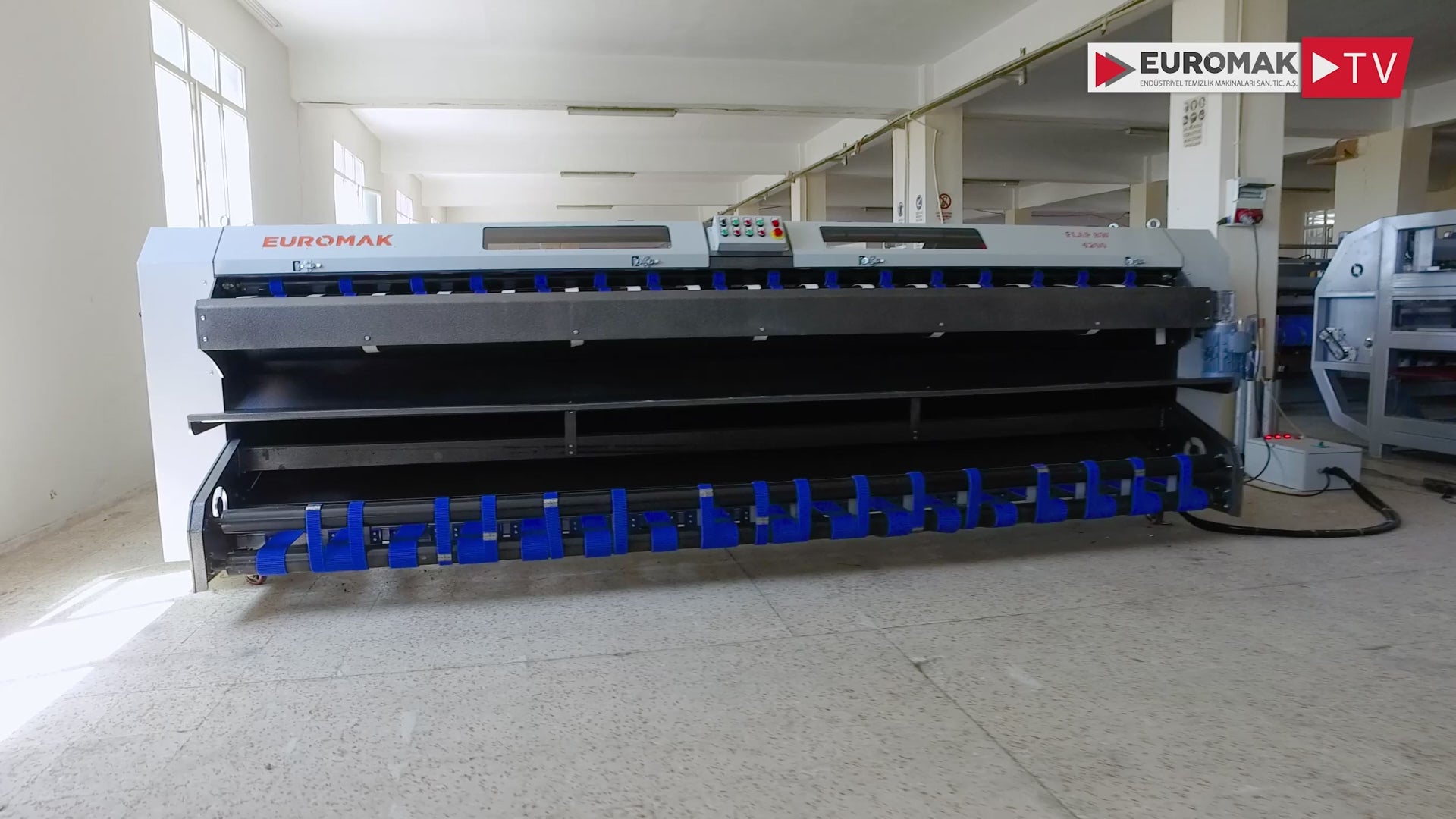
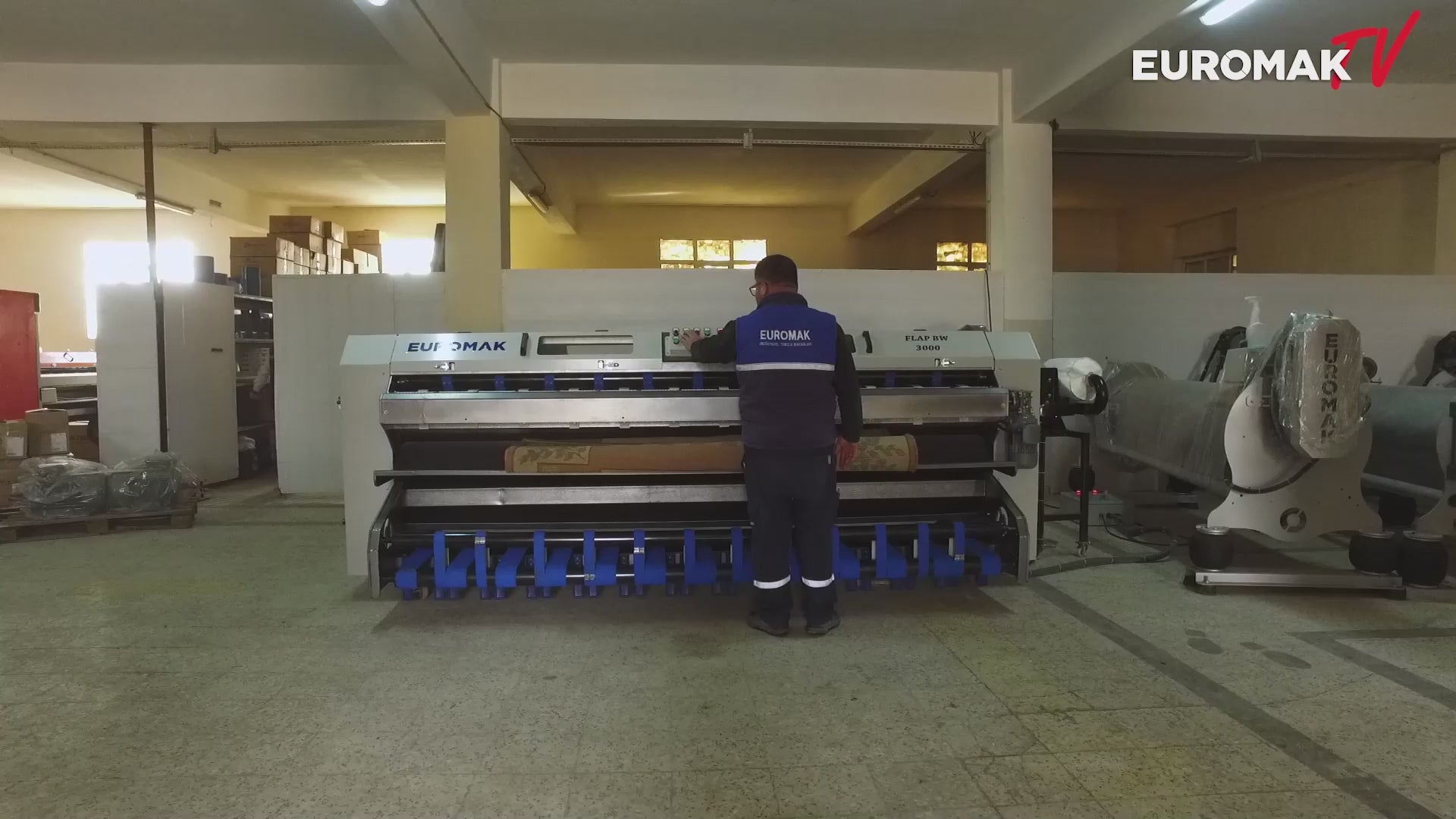
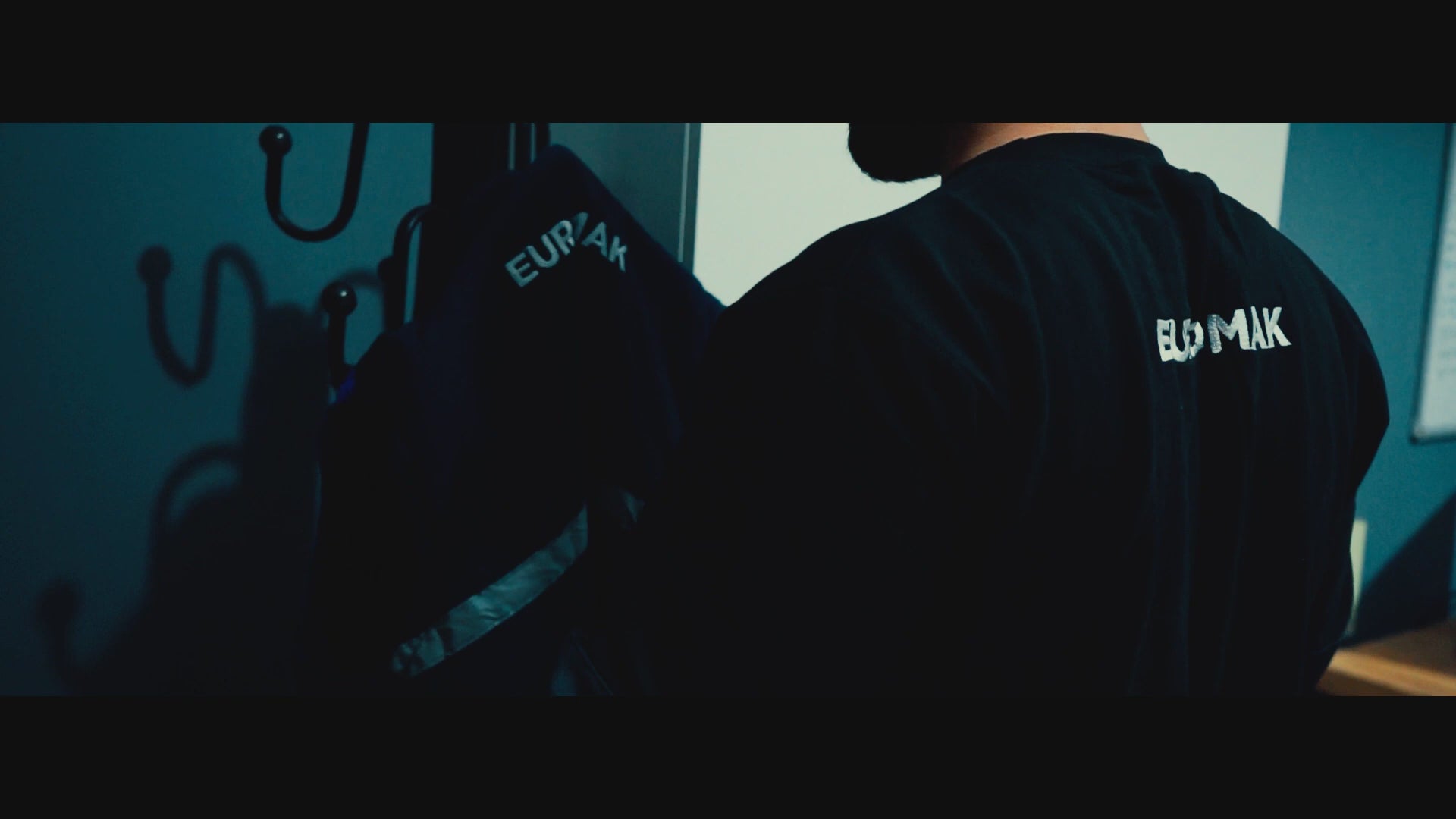
Flap BW 3500 12ft Carpet Rug Duster Dusting Machine
Wide-Format Dusting Power with Superior Cleaning Efficiency
The Euromak Flap BW 3500 is a heavy-duty dust remover machine designed for professional carpet cleaning businesses that demand wider coverage and faster output. Built with industrial-grade materials and precision engineering, it features a dual-beating system, integrated sweeping roller brushes, and high-capacity vacuuming, making it an essential pre-washing solution for large-area rugs and carpets.
The Flap BW rug duster is a powerful upgrade for rug cleaning operations. With its dual beating rollers striking at 208 BPM, built-in sweeping brushes, and industrial-strength vacuum, it effortlessly removes embedded dust, dirt, sand, hair, and micro-bacteria from rugs before washing. Built tough with premium steel and simple controls, it maximizes throughput so you get cleaner carpets faster, reduce manual labor, and elevate service quality. Rug prep becomes simpler, smarter, and more efficient.
Key Features
- Dual Beating Rollers: Applies 208 strikes per minute uniformly across wider carpets to release trapped dust and debris.
- Sweeping Roller Brush System: Equipped with 175 mm (6.9 in) roller brushes that lift and channel particles into the vacuum path.
- Industrial Vacuum Power: High-performance 2,000 m³/hour vacuum (~70,600 ft³/hour) ensures a clean finish by removing loosened particles efficiently.
- Extended Rug Handling: Supports carpets up to 137.8 inches wide (3,500 mm), perfect for large and specialty rugs.
- Enhanced Output: Capable of processing up to 29,600 square feet/day (2,750 m²/day), significantly boosting your daily productivity.
- Adjustable Conveyor Speed: Fine-tune belt speed from 3.2 to 6.5 ft/min (1–2 m/min) for optimal cleaning on all carpet types.
- Durable Construction: Crafted from painted steel, CE-certified, and engineered to exceed industry durability standards.
- User-Friendly Mechanical Panel: Simplified manual control system for reliable, hands-on operation.
Daily Capacity
- 6x8 616 Rugs
- 8x10 370 Rugs
- 9x12 274 Rugs
- 10x14 211 Rugs
- 12x15 Upgrade
Technical Specifications
- Max Carpet Width: 137.8 in / 11.5ft (3,500 mm)
- Belt Width: 142.3 in (3,615 mm)
- Vacuum Power: 2,000 m³/h (~70,600 ft³/h)
- Engine Power: 5.87 kW (~7.8 HP)
- Flapping Speed: 208 beats/min
- Sweeping Roller Diameter: 6.9 in (175 mm)
- Machine Dimensions (W x L x H): 147.6 in x 53.1 in x 60 in
- Weight: 2,645 lbs (1,200 kg)
- Voltage: 3-Phase / 380V / 50Hz
- Control Type: Manual / Mechanical
Financing Options
- 24 months $910 / month
- 36 months $630 / month
- 48 months $490 / month
- 60 months $410 / month
CURRENT LEAD TIME 12—14 Weeks
Frequently Asked Questions
How long is the warranty period for the machines?
All Euromak industrial cleaning machines are backed by a comprehensive 2-year warranty that covers any manufacturing defects or faults in workmanship. This ensures peace of mind from the moment your machine is delivered and installed.
In addition to the standard warranty, Euromak provides an extended 5-year guarantee of spare parts availability and advanced technical support. During this period, customers benefit from priority access to genuine OEM-certified parts, remote diagnostic services, and professional consultations regarding machine usage, maintenance, and optimization.
This long-term support package is designed to ensure uninterrupted operations, minimize downtime, and extend the life and performance of your investment.
How often do machines need maintenance?
Routine maintenance is essential to ensure the long-term performance and reliability of your Euromak machine. Lubrication is required every 200 to 580 operating hours, depending on the specific component and machine model. For example, grooves typically require greasing every 200 hours, while chains and mechanical assemblies require lubrication at approximately 580-hour intervals.
Additionally, daily cleaning of the machine, especially vacuum bags, conveyor systems, and dust chambers, is strongly recommended to prevent buildup and mechanical wear.
Is there training available for operating the machine?
Yes. Once installation is complete, our expert team conducts on-site operational training tailored to your staff’s experience level.
This training covers machine start-up procedures, proper handling techniques, safety protocols, basic troubleshooting, and best practices for maximizing productivity and extending machine lifespan.
Do I need a certified technician for maintenance, or can my team handle it?
Basic maintenance, such as cleaning, lubrication, and routine checks, can be confidently performed by your in-house team using the comprehensive manuals and training provided with every Euromak machine. Our goal is to empower your operators with the knowledge and resources needed for daily and scheduled upkeep.
For more complex servicing or technical issues, Euromak-certified technicians are available for on-site support across the USA and Canada, typically within a 2 to 3 business day response window.
How fast can I get spare parts?
Every machine is delivered with a set of essential spare parts to support seamless operation from day one. To further reduce downtime, we maintain a robust inventory of OEM-certified components at our U.S. distribution center located in Maryland.
We guarantee spare parts availability for a minimum of 5 years after purchase. In-stock items can typically be dispatched within 24 to 48 hours, with actual delivery time depending on your location and selected shipping method.
Our logistics team is committed to ensuring your operation continues without disruption.
What technical support is included after installation?
Following installation, our team will provide continuous technical support to ensure your equipment runs smoothly and efficiently. This includes real-time remote diagnostics to identify and resolve issues, scheduled video consultations with our expert technicians for operational guidance, and personalized usage assistance to help your team maintain optimal performance.
If remote solutions are insufficient, Euromak USA offers on-site service visits, ensuring that more complex needs are addressed promptly and professionally.
Can I access technical documentation and service manuals?
Yes, full documentation is provided with every machine and includes detailed lubrication, cleaning, and troubleshooting instructions.
Are installation services provided with the purchase?
Yes, our team will provide on-site installation after delivery. Once your machines arrive, our team assists with setup to ensure they are properly positioned, connected, and ready for operation.
What happens if the machine breaks down during high season?
We will prioritize requests to minimize operational disruptions for our clients. If a machine experiences a breakdown, remote diagnostics and support are fast-tracked, and spare parts are expedited from our U.S. inventory.
When necessary, a certified technician can be dispatched and typically arrives on-site within 2 to 3 business days, depending on your location.
What are the training options for new staff?
All training for new staff is provided after installation is complete. We want to ensure that your team receives full operational instruction through hands-on, in-person training at your facility. This post-installation training covers every aspect of machine use, safety, and maintenance to ensure your staff can begin working confidently and efficiently from day one.
How long does it take for service personnel to arrive on-site?
Service response times depend on your location, but remote support is typically available immediately to address urgent issues.
If on-site assistance is required, our technician will arrange to visit within 2 to 3 business days for clients in the USA and Canada.
Powering Rug Cleaning Nationwide
Industry pros, from niche boutiques to large-scale cleaning centers, choose Euromak for machinery that keeps business running fast, clean, and smooth.
Euromak USA
Chat With Us
Call us at 1-840-888-9880 or send an email to info@euromakusa.com. Our team is here to help. Or fill out the form below and we will get back to you.
Available Sizes
Machine Highlights
Advanced Dust Removing System
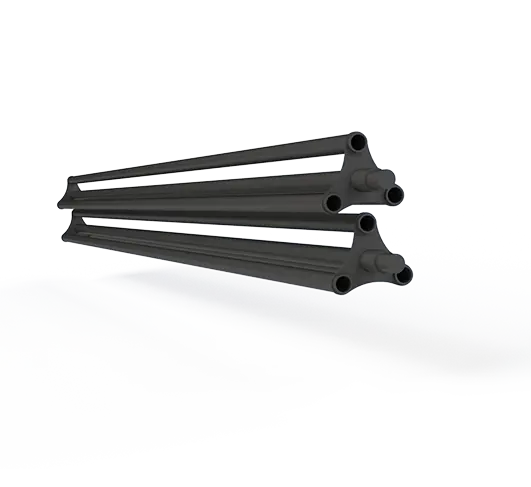
Dual-Dust Beating System
The carpet, positioned in reverse on the belt system, moves through a series of lower and upper beating rollers.
There are two beating rollers, and the system delivers 2 x 208 blows per minute, ensuring every section of the carpet is evenly cleaned.
This thorough beating process effectively removes dust, pile, hair, and other foreign materials that may be embedded in the carpet fibers.
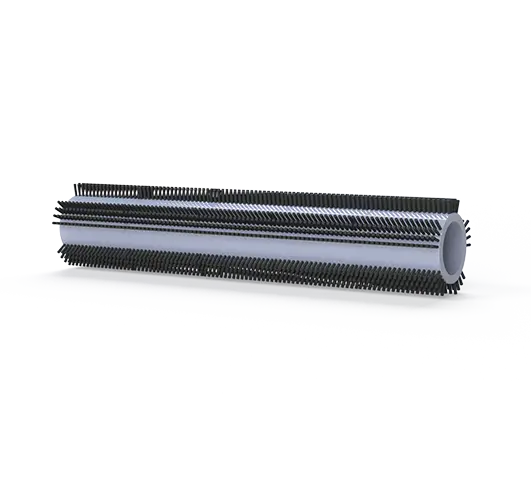
Sweeping Roller Brush
The system includes a specialized roller brush, with a diameter of 175 mm (6.9 inches), designed to remove foreign particles and comb through the carpet.
As the carpet passes through this sweeping brush, it assists in removing substances like adhesives and other residues. This roller brush has been meticulously developed to optimize the combing process for superior cleaning results.
Durable Robust Body
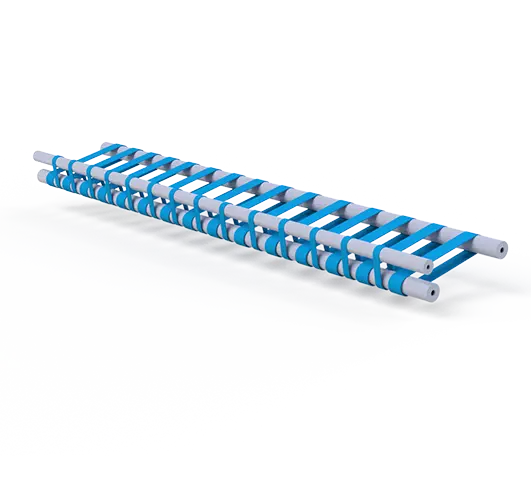
Conveyor Belt
The conveyor belt is engineered for durability and safety, responsible for smoothly moving the carpet through the cleaning stages.
Its two-way belt system allows for the easy handling of heavy carpets, enabling them to be reversed and forwarded with precision using a back-and-forth control mechanism. This ensures carpets that require repeated beating cycles can be efficiently processed.
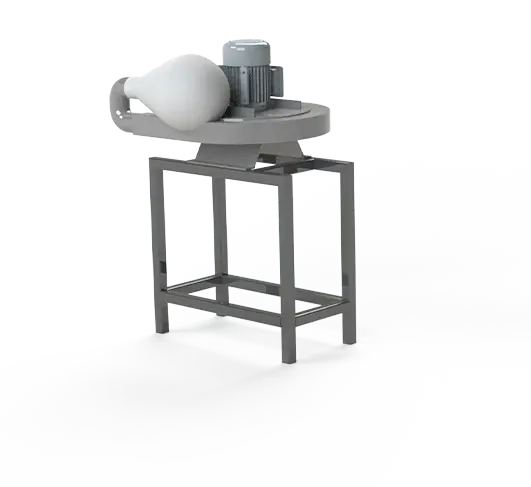
Vacuum System
Once the dust removal and brushing stages are complete, the system's powerful vacuum process kicks in. It efficiently collects hair, bristles, dust, dirt, and other debris from the chamber.
The high-powered vacuum system also prevents the spread of dust particles into the air, maintaining a cleaner environment during operation.
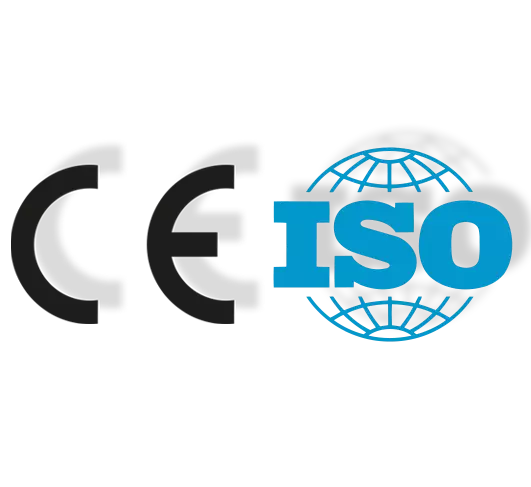
Meets CE Standards
Each machine is manufactured following a stringent quality management system, ensuring compliance with CE standards.
Every stage of production undergoes rigorous testing and certification processes, guaranteeing the highest quality and reliability before the machines are made available for use.
Euromak USA
Warranty & Service Support

Shipping & Installation
We offer our clients all throughout the USA, Canada, and the Caribbean Islands timely door-to-door shipping. Every machine is cautiously handled and packed with protective materials to ensure that it comes in pristine state. Our staff is always ready to help address specific shipment schedules. Once delivered, we guarantee a seamless installation process.
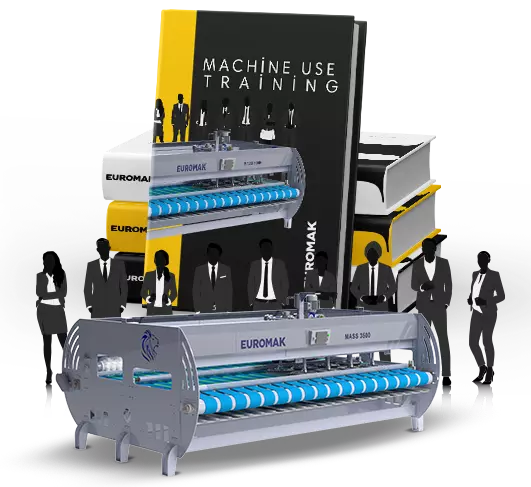
Hands-On Training
Once your equipment is installed, our team will provide full, hands-on training to ensure proper operation and maximize efficiency. Each machine is accompanied by clear maintenance instructions and a recommended service schedule, making it easy to keep your equipment in peak condition. Our ultimate goal is to help you get the most out of your investment and extend the lifespan of your machinery for years to come.

Service & Support
With Euromak, you are backed by a responsive, expert support team. We provide same-day response times and parts delivery within the same week to keep your business moving without delays. From troubleshooting to routine maintenance and training, our dedicated technicians are ready to assist every step of the way.

Rug Cleaning Shop Design & Layout
State-Of-The-Art Rug Cleaning Facility with Euromak
Take your rug carpet cleaning business to the next level with a plant designed for your needs. From start to finish, we’re here to make the process simple and efficient, helping you create a setup that works perfectly for your needs today and grows with you tomorrow.
- Smart Layout Planning: We’ll help you make the most of your space with a layout that’s designed for smooth, productive workflows.
- Right Equipment, Right Fit: We’ll recommend the best machines for your cleaning volume, rug types, and budget.
- See It in 3D: Get a clear view of your setup with detailed 3D designs before you take the next step.
- Room to Grow: Start small and scale up with flexible designs built for your future needs.
- We’re With You All the Way: Our team works closely with you to make sure your plant meets your goals, every step of the way.