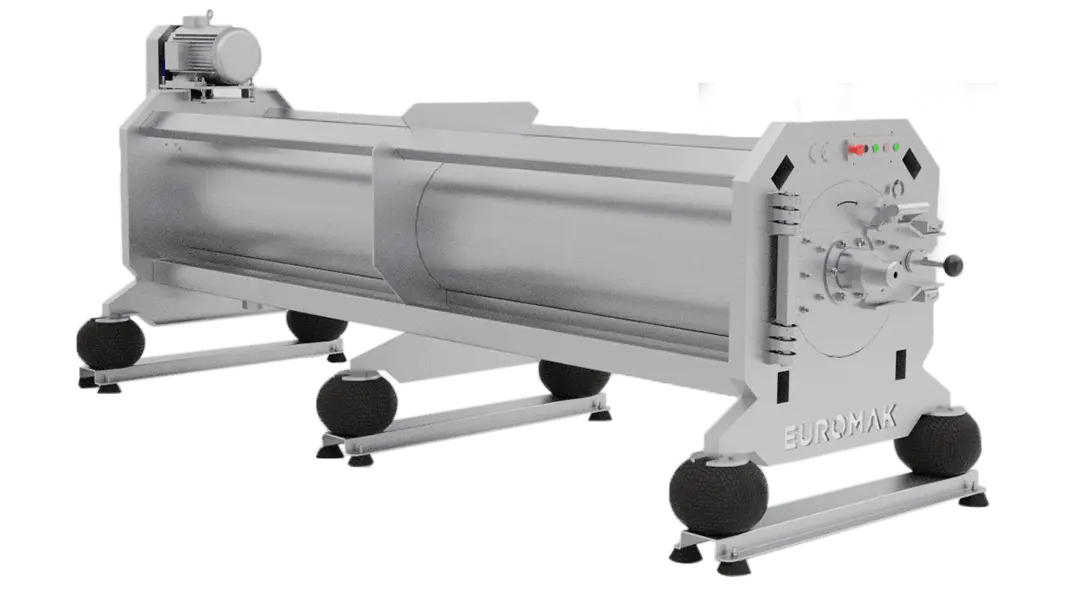
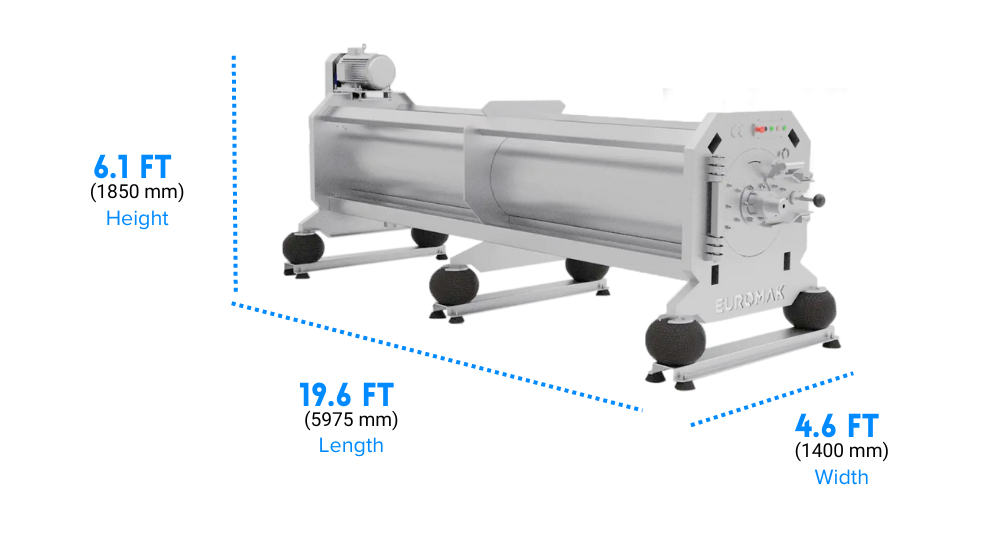
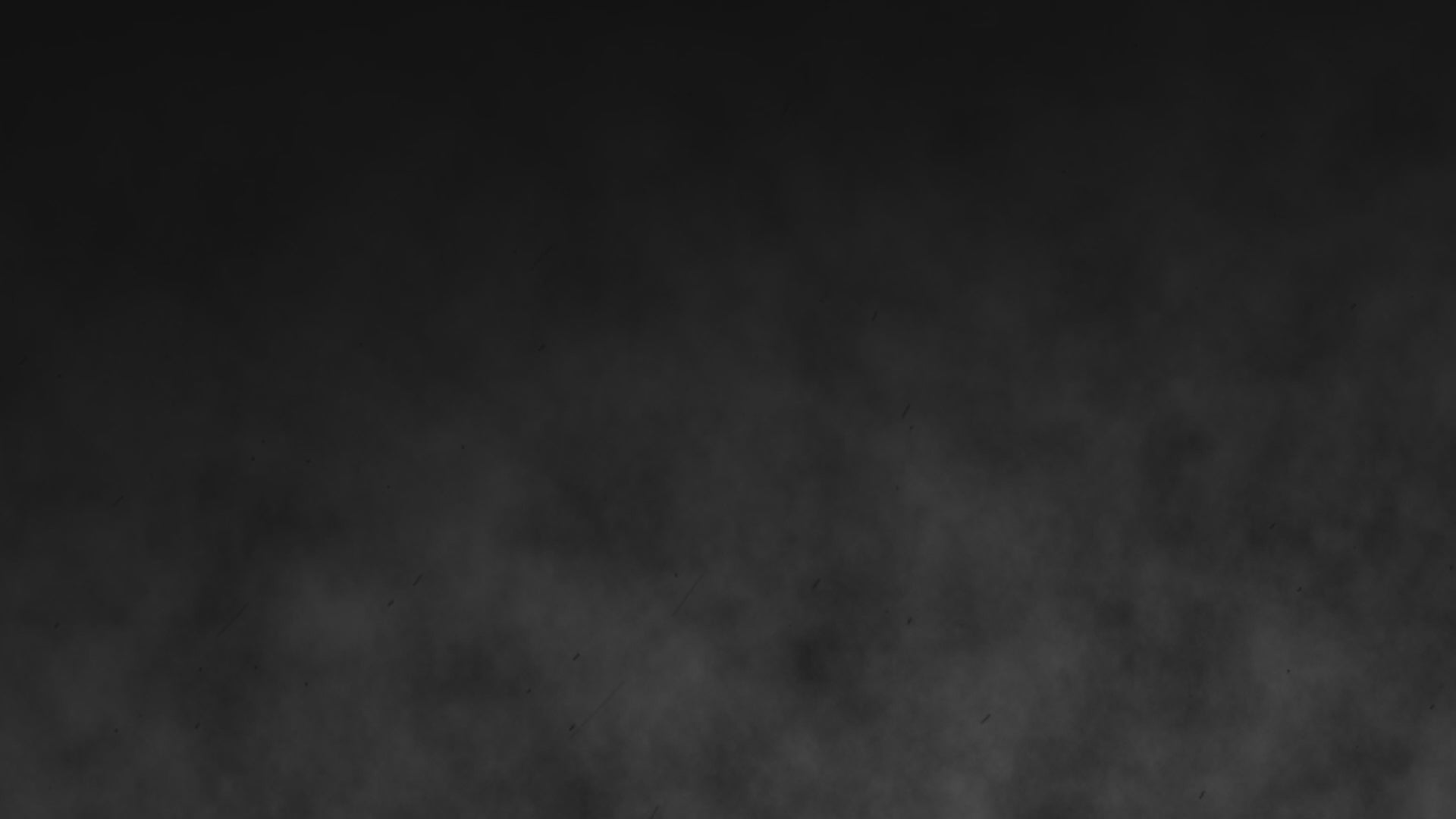
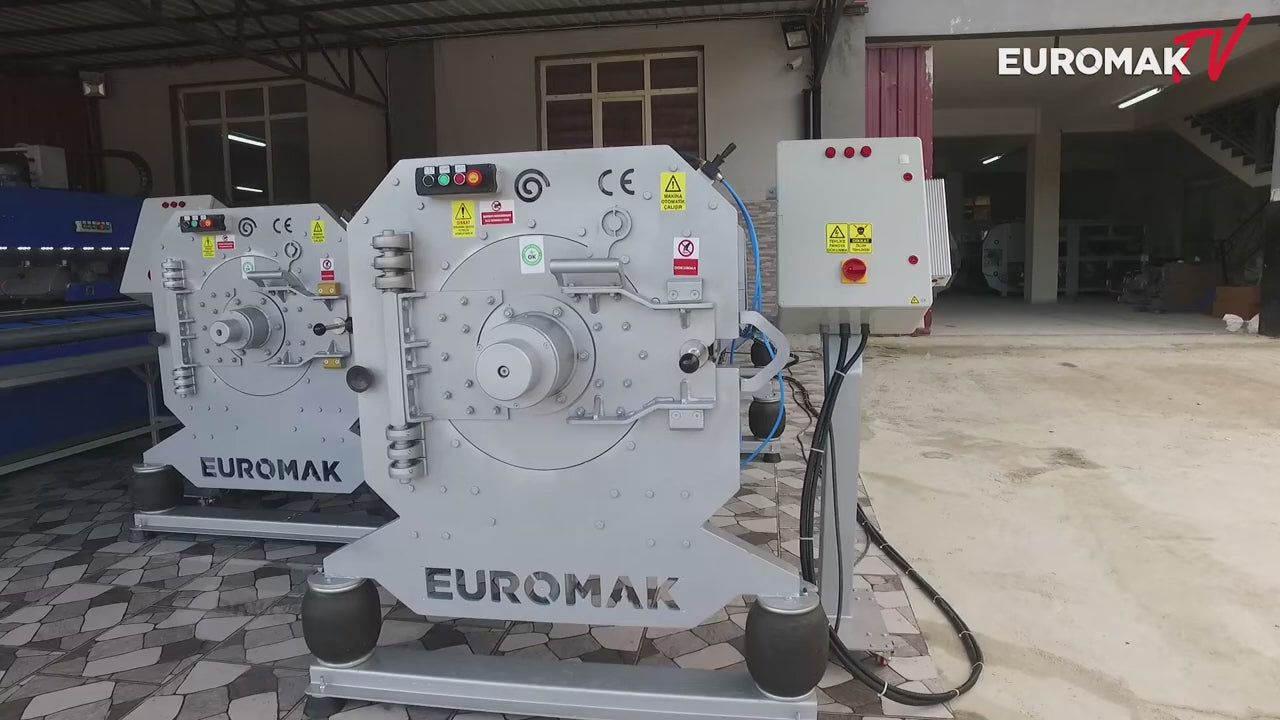


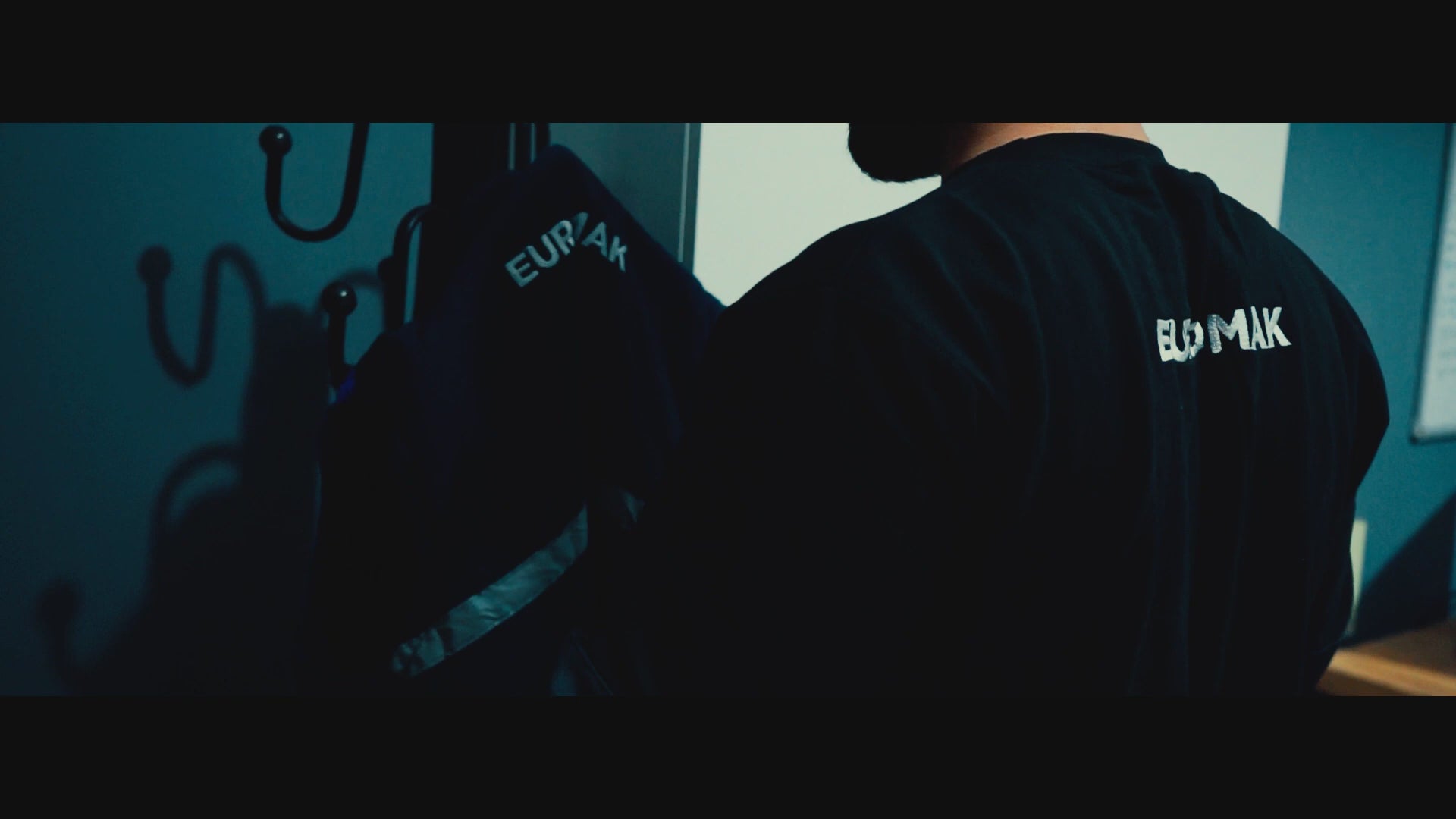
Spin Plus 5200 17ft Rug Centrifuge Machine Wringer Spinner
The Euromak Spin Plus 5200 is the ultimate solution for spinning and drying extra-large rugs and carpets at industrial scale. Built with a 5.2-meter stainless steel drum, high-speed spinning, and a pneumatic cover system, it ensures quick water extraction, minimal drying time, and reliable, safe operation. Ideal for high-volume, large-format carpet and rug cleaning businesses.
Key Features
- Longest Drum in the Series: Boasts a 5,200 mm (204.7 in) long drum with a 475 mm (18.7 in) diameter—designed for oversized rugs and carpets.
- Optimized for Efficiency: Spins at 900 RPM, extracting up to 90% of water from carpets and rugs in a matter of minutes.
- Top-Tier Daily Capacity: Handles up to 37,674 ft²/day (3,500 m²/day), supporting large-scale operations with continuous performance.
- Stainless Steel Drum Construction: Ensures high durability and hygienic performance under constant exposure to moisture and chemicals.
- Pneumatic Safety Cover: Securely locks the lid during operation for operator safety and spinning stability.
- Speed Control System: Allows for adjustable spinning speed based on rug or carpet type.
- Dual Operation Modes: Manual and automatic control options to suit workflow preferences.
Daily Capacity
- 8x10 470 Rugs
- 9x12 348 Rugs
- 10x14 269 Rugs
- 12x15 209 Rugs
Technical Specifications
- Inner Drum Length: 204.7 in / 17ft (5,200 mm)
- Inner Drum Diameter: 18.7 in (475 mm)
- Max Rug/Carpet Width: 204.7 in / 17ft (5,200 mm)
- Spinning Speed: 900 RPM
- Engine Power: 15 kW (~20.1 HP)
- Daily Capacity: 37,674 ft² (3,500 m²)
- Suspension Quantity: 12
- Speed Control: Included
- Control Panel: Manual / Automatic
- Cover System: Pneumatic
- Machine Dimensions (W x L x H): 55.1 in x 235.2 in x 72.8 in
- Weight: 2,535 lbs (1,150 kg)
- Voltage: 3-Phase / 380V / 50Hz
- Material: Galvanized frame with stainless steel inner drum
- Certification: CE Certified
Financing Options
- 24 months $1,280 / month
- 36 months $887 / month
- 48 months $680 / month
- 60 months $560 / month
CURRENT LEAD TIME 12—14 Weeks
Frequently Asked Questions
How long is the warranty period for the machines?
All Euromak industrial cleaning machines are backed by a comprehensive 2-year warranty that covers any manufacturing defects or faults in workmanship. This ensures peace of mind from the moment your machine is delivered and installed.
In addition to the standard warranty, Euromak provides an extended 5-year guarantee of spare parts availability and advanced technical support. During this period, customers benefit from priority access to genuine OEM-certified parts, remote diagnostic services, and professional consultations regarding machine usage, maintenance, and optimization.
This long-term support package is designed to ensure uninterrupted operations, minimize downtime, and extend the life and performance of your investment.
How often do machines need maintenance?
Routine maintenance is essential to ensure the long-term performance and reliability of your Euromak machine. Lubrication is required every 200 to 580 operating hours, depending on the specific component and machine model. For example, grooves typically require greasing every 200 hours, while chains and mechanical assemblies require lubrication at approximately 580-hour intervals.
Additionally, daily cleaning of the machine, especially vacuum bags, conveyor systems, and dust chambers, is strongly recommended to prevent buildup and mechanical wear.
Is there training available for operating the machine?
Yes. Once installation is complete, our expert team conducts on-site operational training tailored to your staff’s experience level.
This training covers machine start-up procedures, proper handling techniques, safety protocols, basic troubleshooting, and best practices for maximizing productivity and extending machine lifespan.
Do I need a certified technician for maintenance, or can my team handle it?
Basic maintenance, such as cleaning, lubrication, and routine checks, can be confidently performed by your in-house team using the comprehensive manuals and training provided with every Euromak machine. Our goal is to empower your operators with the knowledge and resources needed for daily and scheduled upkeep.
For more complex servicing or technical issues, Euromak-certified technicians are available for on-site support across the USA and Canada, typically within a 2 to 3 business day response window.
How fast can I get spare parts?
Every machine is delivered with a set of essential spare parts to support seamless operation from day one. To further reduce downtime, we maintain a robust inventory of OEM-certified components at our U.S. distribution center located in Maryland.
We guarantee spare parts availability for a minimum of 5 years after purchase. In-stock items can typically be dispatched within 24 to 48 hours, with actual delivery time depending on your location and selected shipping method.
Our logistics team is committed to ensuring your operation continues without disruption.
What technical support is included after installation?
Following installation, our team will provide continuous technical support to ensure your equipment runs smoothly and efficiently. This includes real-time remote diagnostics to identify and resolve issues, scheduled video consultations with our expert technicians for operational guidance, and personalized usage assistance to help your team maintain optimal performance.
If remote solutions are insufficient, Euromak USA offers on-site service visits, ensuring that more complex needs are addressed promptly and professionally.
Can I access technical documentation and service manuals?
Yes, full documentation is provided with every machine and includes detailed lubrication, cleaning, and troubleshooting instructions.
Are installation services provided with the purchase?
Yes, our team will provide on-site installation after delivery. Once your machines arrive, our team assists with setup to ensure they are properly positioned, connected, and ready for operation.
What happens if the machine breaks down during high season?
We will prioritize requests to minimize operational disruptions for our clients. If a machine experiences a breakdown, remote diagnostics and support are fast-tracked, and spare parts are expedited from our U.S. inventory.
When necessary, a certified technician can be dispatched and typically arrives on-site within 2 to 3 business days, depending on your location.
What are the training options for new staff?
All training for new staff is provided after installation is complete. We want to ensure that your team receives full operational instruction through hands-on, in-person training at your facility. This post-installation training covers every aspect of machine use, safety, and maintenance to ensure your staff can begin working confidently and efficiently from day one.
How long does it take for service personnel to arrive on-site?
Service response times depend on your location, but remote support is typically available immediately to address urgent issues.
If on-site assistance is required, our technician will arrange to visit within 2 to 3 business days for clients in the USA and Canada.
Powering Rug Cleaning Nationwide
Industry pros, from niche boutiques to large-scale cleaning centers, choose Euromak for machinery that keeps business running fast, clean, and smooth.
Euromak USA
Contact Us
Call us at 1-840-888-9880 or send an email to info@euromakusa.com. Our team is here to help. Or fill out the form below and we will get back to you. Hours: Monday - Friday 9am to 5pm EST
Available Sizes
Spin 2700 9ft Rug Spinner Centrifuge Machine
If you have any questions, you are always welcome to contact us. We'll get back to you as soon as possible, within 24 hours on weekdays.
-
Shipping Information
Use this text to answer questions in as much detail as possible for your customers.
-
Customer Support
Use this text to answer questions in as much detail as possible for your customers.
-
FAQ’s
Use this text to answer questions in as much detail as possible for your customers.
-
Contact Us
Use this text to answer questions in as much detail as possible for your customers.
Euromak Spinner
Superior Corrosion Resistance
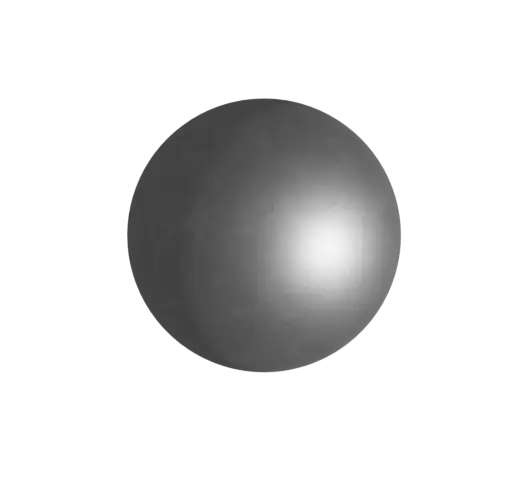
Galvanized Frame + Stainless Steel Drum
Euromak centrifuge machines are constructed using industrial-grade materials selected for strength, durability, and resistance to moisture and wear. The inner drum is made of high-quality stainless steel, which resists corrosion and maintains hygiene, essential for continuous carpet processing.
The outer frame and structural components are built from galvanized steel, providing robust protection against rust and environmental damage. This rugged construction ensures long-term reliability even under heavy daily use. The entire unit is engineered above industry standards in thickness and assembly quality.
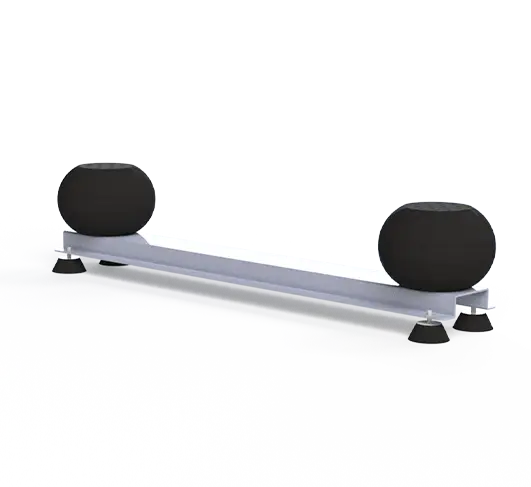
Suspension System
Euromak centrifuge carpet spinning machines feature an advanced multi-point suspension system. This system absorbs high-speed vibrations generated during the 900–1200 RPM spin cycles, ensuring machine stability and operator safety.
The reduced vibration enhances the longevity of critical components such as the motor, bearings, and drum, while also decreasing noise and wear. This design not only ensures smoother and quieter operation but also protects the carpets during drying.
By minimizing mechanical stress, the suspension system contributes significantly to the machine’s 10+ year performance durability and consistent drying efficiency.
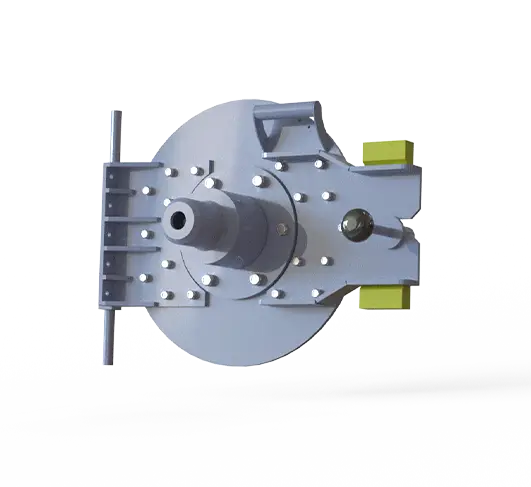
Pneumatic Door System
Equipped with a pneumatic cover system that significantly enhances safety, ease of use, and operational efficiency.
The automated door mechanism uses compressed air to open and close the lid securely, reducing manual effort and preventing accidental opening during operation. This system is synchronized with the carpet rewinding and vacuum process to ensure a easy workflow.
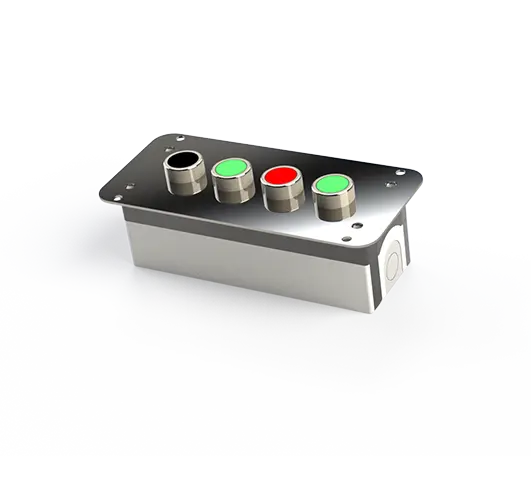
Control System
Euromak centrifuge machines are designed with a dual-mode control system, offering both automatic and manual operation for maximum flexibility.
This user-friendly interface allows operators to easily switch modes depending on operational needs or skill levels. In automatic mode, the system manages the spinning cycle, cover actuation, and safety interlocks with precision—minimizing human error and ensuring consistent performance.
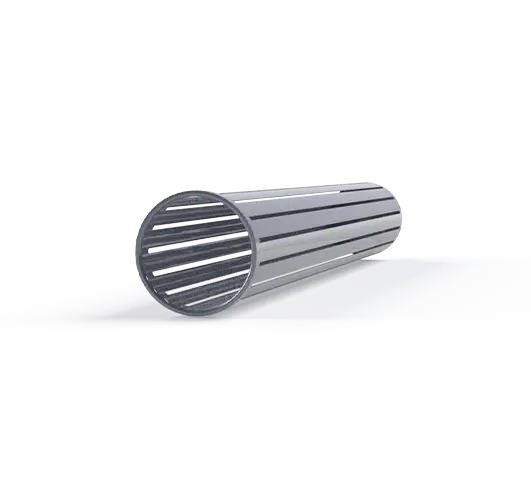
Stainless-Steel Drum
The inner drum of Euromak centrifuge carpet spinning machines is built from durable stainless steel, designed for long-lasting, hygienic operation.
Depending on the model, the drum length ranges from approximately 106 to 205 inches, with diameters up to 18.7 inches. This spacious design allows for efficient spinning of large carpets, improving daily capacity and drying performance. The drum is precision-balanced to minimize vibration during high-speed spins, which reach up to 1,200 RPM.
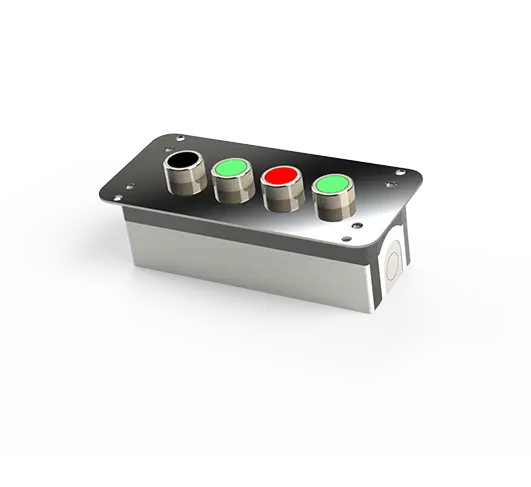
Speed Control
Euromak centrifuge machines include an advanced speed control system that allows operators to adjust spinning speeds according to carpet type and moisture level.
This flexibility is critical for balancing effective water extraction with carpet care. Spin speeds range up to 1,200 RPM, and the control system ensures smooth acceleration and deceleration, reducing mechanical stress on the motor and internal components.
By fine-tuning the RPM, operators can handle delicate rugs or thicker materials with precision, minimizing wear and extending carpet life.
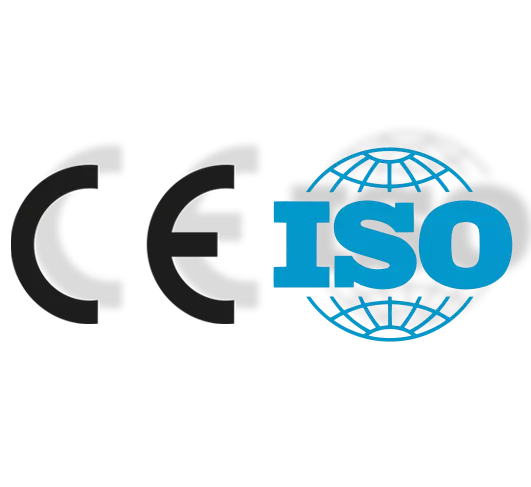
Quality Management System
A comprehensive quality management system is implemented at every stage of production, ensuring that all machines are manufactured in compliance with CE standards. Rigorous testing and certification processes are conducted to guarantee that each machine is ready for use without compromising on quality, performance, or safety.
Euromak USA
Warranty & Service Support

Shipping & Installation
We offer our clients all throughout the USA, Canada, and the Caribbean Islands timely door-to-door shipping. Every machine is cautiously handled and packed with protective materials to ensure that it comes in pristine state. Our staff is always ready to help address specific shipment schedules. Once delivered, we guarantee a seamless installation process.
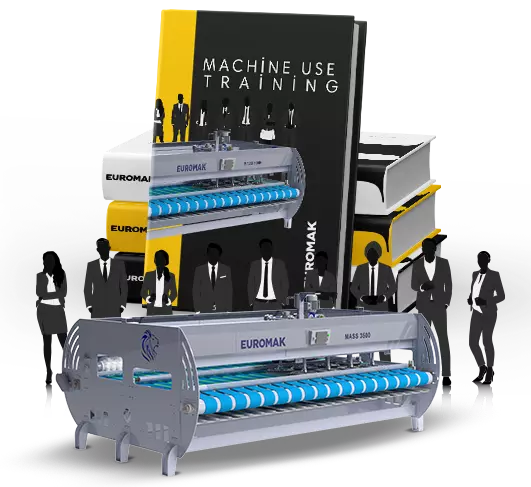
Hands-On Training
Once your equipment is installed, our team will provide full, hands-on training to ensure proper operation and maximize efficiency. Each machine is accompanied by clear maintenance instructions and a recommended service schedule, making it easy to keep your equipment in peak condition. Our ultimate goal is to help you get the most out of your investment and extend the lifespan of your machinery for years to come.

Service & Support
With Euromak, you are backed by a responsive, expert support team. We provide same-day response times and parts delivery within the same week to keep your business moving without delays. From troubleshooting to routine maintenance and training, our dedicated technicians are ready to assist every step of the way.

Rug Cleaning Shop Design & Layout
State-Of-The-Art Rug Cleaning Facility with Euromak
Take your rug carpet cleaning business to the next level with a plant designed for your needs. From start to finish, we’re here to make the process simple and efficient, helping you create a setup that works perfectly for your needs today and grows with you tomorrow.
- Smart Layout Planning: We’ll help you make the most of your space with a layout that’s designed for smooth, productive workflows.
- Right Equipment, Right Fit: We’ll recommend the best machines for your cleaning volume, rug types, and budget.
- See It in 3D: Get a clear view of your setup with detailed 3D designs before you take the next step.
- Room to Grow: Start small and scale up with flexible designs built for your future needs.
- We’re With You All the Way: Our team works closely with you to make sure your plant meets your goals, every step of the way.